In order to prevent damage to a bridge’s structure, there are many that may only be driven over by vehicles up to a certain permissible weight and solutions are needed to identify these vehicles. Volkmann Strassen- und Verkehrstechnik GmbH, a leading company in the field of road and construction site safety, uses Blickfeld Cube 1’s 3D LiDAR sensors to play an important role in their solution to this issue. The device identifies such vehicles and safely diverts them before they cross and cause further damage to the structure.
Weight measurement during free travel (Weigh in Motion)
In practice, it would not be feasible to measure each vehicle individually off the track on a static scale, because the traffic flow would come to a standstill, or at least cause delays and congestion. Therefore, weight measurement must take place while the vehicle is in motion. However, this presents technical challenges – not only in clearly assigning the weight to a vehicle, but also in taking photos of the license plates of vehicles that are too heavy, which are required as evidence for the authorities. The unambiguous assignment of a weight to the correct vehicle is very important for data protection reasons, so that only photos of vehicles that are too heavy (and thus no photos of vehicles that comply with the regulations) are taken. Volkmann Strassen- und Verkehrstechnik GmbH has consequently developed a measuring system consisting of several components that avoid such issues.
Structure of the measuring system
By using the measuring system from Volkmann Strassen- und Verkehrstechnik GmbH, (consisting of a scale, one to two Blickfeld Cube 1 LiDAR sensors per ten meters of track and a camera), the weight measurement, which is carried out by a camera, takes place directly on the road while the vehicle is moving, usually on a track limited to a speed of 40 – 80 km/h. Currently, a track length of 35 meters is being tested with five Blickfeld LiDAR sensors to clearly determine the weight of a vehicle and trigger a camera photo of the license plate. A flat scale is integrated into the roadway at the beginning of this detection section and as soon as the weight hits the scale during an axle crossing, the scale triggers a weighing process. The total weight of a vehicle is determined from the individual values measured per axle. The challenge here is that the scale cannot determine how many vehicles the axles belong to, since not all cars have two axles. For example, a car with a trailer may have three or four axles, and a truck may have four, eight or more. So how does the system know if the measured weight belongs to one, two, or even more vehicles in a row?
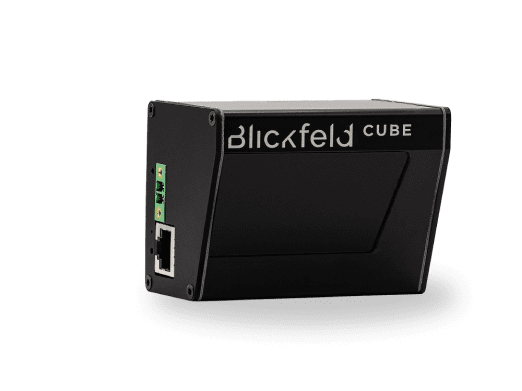
How to detect several vehicles in the measuring system?
This is where the capabilities of the Blickfeld Cube 1 LiDAR sensors come into play. They record the entire test field three-dimensionally, so it can recognise how many, and what type of vehicles whether that be cars, trucks, cars with caravans, vans, motorcycles, etc. – are in which position on the measurement track at any given time, and to which the respective measured weight can be assigned when an axle is crossed. Based on this combined information – weight plus assignment to a vehicle – an identification number (ID) can now be assigned to each vehicle. This ID is the prerequisite for the system to trigger the camera when a vehicle exceeds the permissible total weight. Since LiDAR sensors record the scene anonymously, the right to protection of drivers’ personal data is upheld at all times.
From test to practice
Given the measurement system was recently tested very successfully on a private company site, Volkmann Strassen- und Verkehrstechnik GmbH will be putting it into practice for the first time this year on a federal highway to protect bridges there from overloading. Taking the large number of weight-restricted bridges in Germany into consideration – 2700 alone are considered in need of refurbishment and are scheduled for modernization by 2030 – with rapid expansion to other locations is likely.