- The research aims to develop a train shunting assistance system based on an advanced sensor set including Blickfeld LiDAR technology
- It represents a significant step forward to safe and efficient shunting of freight trains and allows for the introduction of autonomous features
- Reliable and accurate automated detection of objects on the tracks helps avoid collision without exposing workers to hazards
Blickfeld, a leading LiDAR sensor technology company, enables groundbreaking research and developments in the autonomous railway space by providing its sensor solutions to FH Aachen, one of Germany’s foremost Universities of Applied Scienes. FH Aachen is using the Blickfeld sensors as part of a consortium working in an EU-funded project named SAMIRA (Shunting Assistant & Monitoring Interface for Autonomous Rail Applications) researching the difficult task of shunting freight trains. Nowadays, shunting usually requires an assistant standing on the platform of the last wagon, who, among other things, reports by radio any obstacles that might affect the train’s pathway. This particular role is dangerous and having to work outdoors in all weather conditions, makes the role hard to fill.
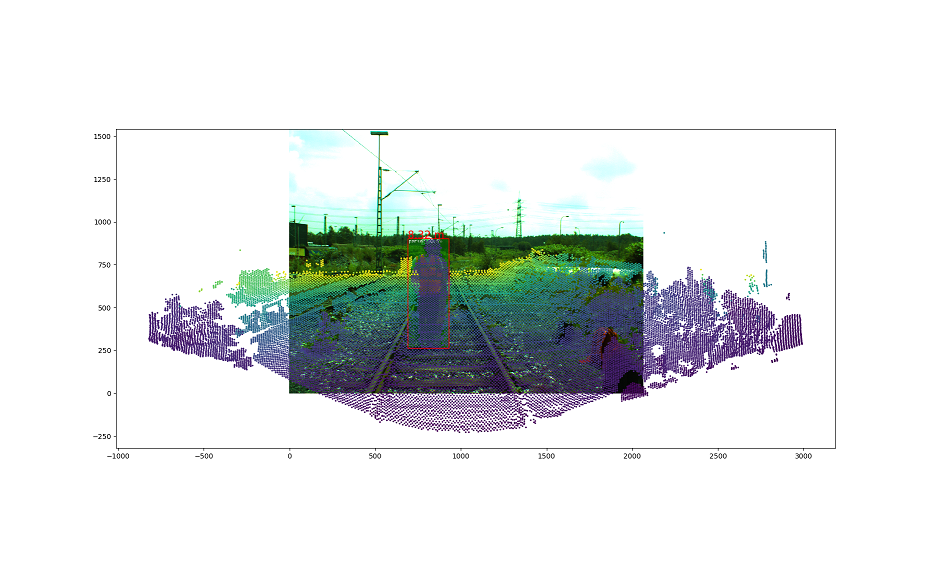
The shunting assistance system researched in this project relies on an advanced sensor set including Blickfeld´s innovative LiDAR technology which allows the train driver to see the environment behind the train from the driver’s cab accurately, reliably, and three-dimensionally, using laser technology to detect objects on the tracks. Thus, 3D LiDAR sensors enable safe automated shunting and help to avoid collisions – all without exposing employees to adverse conditions and hazards. As a result, the process is much more efficient, faster, and safer.
Reliable track monitoring even in curves
The assistance system developed takes over track monitoring by integrating Blickfeld’s solid-state 3D LiDAR sensors Cube 1 with a large field of view of 70 degrees and Cube Range 1 for extra-long-distance detection of up to 150 meters. This proves to be ideal when keeping an eye on the track area, even when driving through curves. Blickfeld’s software-defined LiDAR sensors can be customized to any field of view and solution that a customer would require. This makes them particularly suitable for this task, as they can be used flexibly in different application scenarios without the need for complex modifications to the hardware. In addition to this, Blickfeld’s solid-state, semiconductor-based sensing technology is highly robust, which means it can withstand the strong vibrations caused by everyday railroad operations.
Advanced sensor set for reliable perception
The Blickfeld LiDAR sensors are integrated into a set of other sensors whose measurement results are compared with each other, and each provides additional information: a stereo camera for close-range detection, two additional cameras providing the data basis for algorithm-based object detection, as well as a radar sensor. This system provides a fusion of camera images and 3D point clouds, which enables the exact detection of objects with redundant mutual control of the different sensor types. The extracted information is later translated into a live feed via a tablet, which is situated with the driver – indicating whether there are people, signals, vehicles, or any other objects in the monitored area.
Matthias Blumenschein, part of FH Aachen’s Rail Vehicle Engineering Research Team says, “Blickfeld’s LiDAR sensor technology is exactly what we are looking for in terms of resolution, field of view, and price. The potential for this technology to provide a dramatic increase in both efficiency and safety is significant. We are pleased to have made great progress in researching train shunting within the SAMIRA project, which is now nearing completion, and we plan to look at even more exciting aspects in follow-up projects.”
Florian Petit, co-founder and Chief Experience Officer at Blickfeld says, “Equipping such a pioneering team at FH Aachen with our LiDAR sensors is a pleasure. It is always exciting to see the application of our technology helping major industries to take steps toward the future. In addition to the immediate benefits such as operational efficiency and personnel safety, the introduction of autonomous functions also has broader implications, e.g. they promote the smooth running of the entire train operation and thus help to make the environmentally-friendly train transport more attractive to the logistics industry.
The research project is EU funded The research project SAMIRA (Shunting Assistant & Monitoring Interface for Autonomous Rail Applications), which is funded by the European Regional Development Fund 2014-2020 as part of the NRW Lead Market Competition “Mobility and Logistics EFRE-0801689)
Read the case story: https://www.blickfeld.com/case-studies/fh-aachen/