LiDAR-Systeme haben in der Vergangenheit mit einigen Probleme zu kämpfen gehabt: Sie waren weder performant, noch robust genug für den Einsatz in der Automobilindustrie. Ein noch viel größeres Problem stellten allerdings bisher die Kosten für ein LiDAR-System dar: Die Sensoren waren viel zu teuer für den Massenmarkt Automobil. Dieses Problem ist Blickfeld angegangen. Die Technologie des Münchener Start-ups setzt auf MEMS-Spiegel und hochautomatisierte Fertigung – und bereitet so dem autonomen Fahrzeug den Weg.
Das Problem: Fehlende Robustheit und zu hohe Produktionskosten
Die LiDAR-Technologie ist keine neue Erfindung, sie kommt bereits seit den 60er Jahren in verschiedenen Anwendungen zum Einsatz, etwa zur Messung von Emissionen in der Atmosphärenforschung oder zur Fernerkundung in der Archäologie. Doch die LiDAR-Systeme standen bisher vor einigen gravierenden Probleme:
- LiDAR-Systeme sind bisher sehr groß.
- Die eingesetzte Mechanik ist empfindlich gegenüber rauen Umweltbedingungen wie Erschütterungen, Vibrationen, Hitze und Kälte.
- Die Reichweite der bisherigen LiDAR-Systeme reicht für viele Anwendungen nicht aus.
- Und: LiDAR-Sensoren sind heute weder in großen Stückzahlen noch zu erschwinglichen Preisen verfügbar.
All diese Punkte stellen besonders für die Automobilindustrie große Probleme dar, die händeringend nach leistungsfähigen LiDAR-Systemen mit robustem und produktionsskalierbarem Design sucht. Warum? Weil LiDAR essentiell für die autonom fahrenden Autos von morgen ist. In der Mobilität geht es immer um Abstände und Geschwindigkeiten. Nicht-Kollidieren ist essentiell im Straßenverkehr. LiDAR Sensoren erfassen unmittelbar und sicher. Experten gehen daher davon aus, dass zukünftig gleich mehrere LiDAR-Sensoren je Auto verbaut sein werden. Hierfür müssen aber zunächst die genannten Probleme überwunden werden.
Woher stammen die Probleme?
Klassische, mechanisch drehende LiDAR-Konzepte sind empfindlich und komplex im Aufbau und in der Fertigung, was zu großen Abmessungen und einem hohen Preis führt. Andere Technologien und Bauarten wie beispielsweise Optical-Phased-Array- und Flash-LiDAR haben zwar durchaus das Potenzial, deutlich weniger Bauraum zu benötigen und günstiger produziert werden zu können, sind aber noch am Anfang der Entwicklung oder haben systembedingte Nachteile, etwa eine sehr begrenzte Reichweite.
Die Lösung: MEMS-basierte LiDAR Sensoren
Eine vielversprechende Lösung stellen dagegen LiDAR-Sensoren dar, die auf MEMS-Spiegeln basieren. Ihre Siliziumbauweise ist bereits deutlich fortgeschritten und in vielen Anwendungen im Automobil sehr erfolgreich in Verwendung. Zudem kommt die MEMS-Technologie ohne rotierende Bauteile aus und ist daher viel robuster und langlebiger als die mechanischen LiDAR-Systeme. Auf dem Markt verfügbare MEMS-Spiegel zur Ablenkung der Laserstrahlen haben kleine Spiegelgrößen und kleine Ablenkwinkel, da diese für ihre bisherige Verwendung ausreichten. Ihre Leistung in Bezug auf die Reichweite und das abgedeckte Sichtfeld ist daher eingeschränkt.
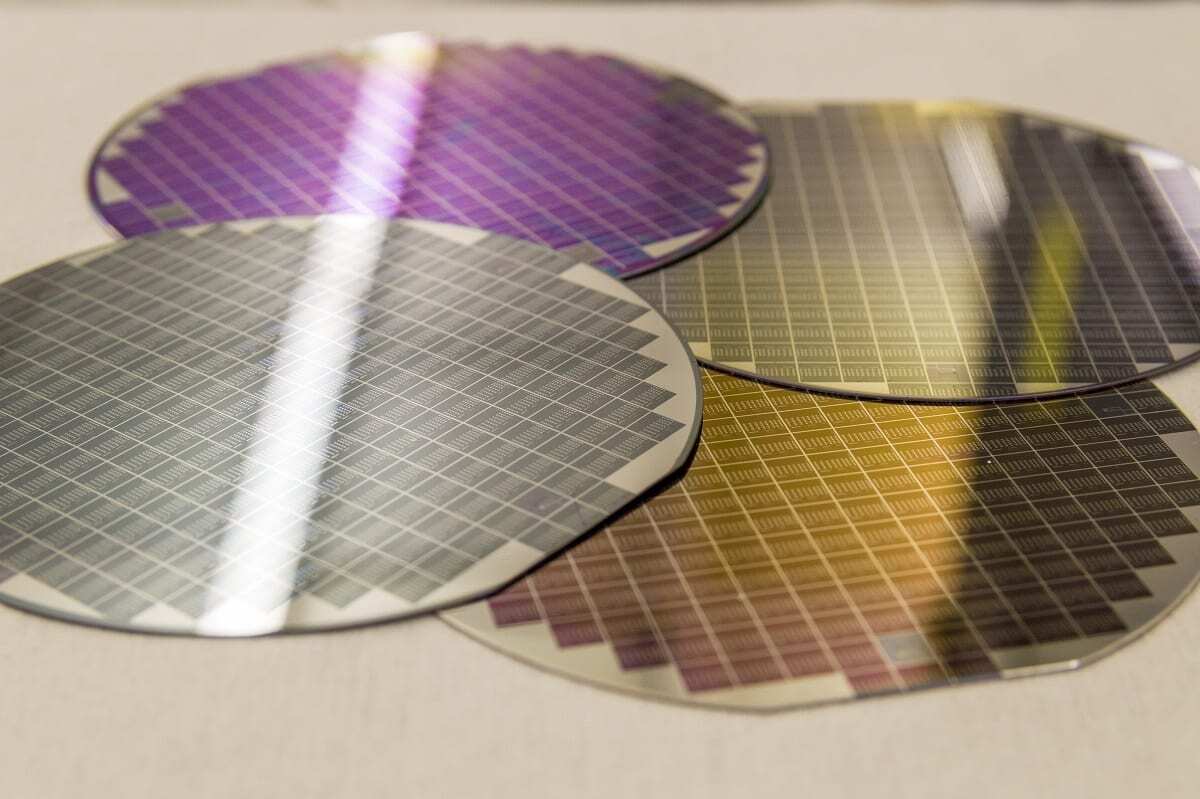
Die Blickfeld-Lösung: Besonders große MEMS-Spiegel
Auch Blickfeld setzt auf MEMS-basierte LiDAR-Systeme. Doch was macht das Unternehmen anders? Um die Reichweite der Sensoren zu erweitern, hat Blickfeld eigens MEMS-Spiegel entwickelt. Mit großzügigen Abmessungen von mehr als 10 Millimetern Spiegeldurchmesser kann somit ein hoher Anteil an einfallendem Licht auf den Fotodetektor gelenkt werden. So erkennt der LiDAR in mehr als 180 Metern Entfernung noch sicher sogar schwach reflektierende Objekte. Im Vergleich dazu verfügen herkömmliche MEMS-Spiegel über Durchmesser von nur wenigen Millimetern und kleine Ablenkwinkel, was beim Einsatz in LiDARs die Reichweite und das Sichtfeld entsprechend verkleinert.
Weitere Vorteile des in Blickfeld-Produkten verbauten MEMS-Spiegel sind:
- eine große Auslenkung, was einen Scanwinkel von ca 100° x 30° und damit ein breites Sichtfeld ermöglicht.
- Räumliche Filterwirkung durch koaxialen Aufbau: Das vom Laser ausgesendete und vom MEMS-Spiegel auf die Szenerie abgelenkte Licht wird nach der Reflexion an den Objekten im Feld auf einem optisch nahezu identischen Weg zurück auf den Detektor geleitet. Damit werden Lichtphotonen nur aus exakt der Richtung eingesammelt, in welche der Laser gesendet hat. Dadurch wird das Hintergrundlicht, etwa durch Sonne oder andere LiDARs minimiert und es entsteht ein sehr hohes Signal-Rausch-Verhältnis, was der Reichweite zugutekommt.

Wie begegnet Blickfeld dem Problem der Produktion?
Die von Blickfeld entwickelten MEMS-Spiegel lösen drei der vier genannten Probleme: Die LiDARs sind platzsparend, robust und performant. Wie begegnet Blickfeld aber dem Problem der kostenintensiven Herstellung? Indem es die Spiegel mit kostengünstigen fotolithografischen Produktionstechniken herstellt, die höchste Präzision bei extremer Skalierbarkeit ermöglichen, sogenannter MEMS Siliziumfertigung. Aus einem Standard-Silizium-Wafer mit einem Durchmesser von 200 Millimetern entstehen hochautomatisiert hunderte MEMS-Bauteile gleichzeitig. Die in der Halbleiterindustrie bereits seit Jahrzehnten erprobte und etablierte Methode verhilft der Technologie in den Massenmarkt.
Der MEMS-Spiegel ist dabei in einen Aufbau aus ‚commercial off-the-shelf‘, also handelsüblichen Standardkomponenten eingebettet. Dank dieser am Markt verfügbaren Laser- und Detektoreinheiten ist eine kostengünstige und skalierbare Produktion der Sensoren möglich.
Autonom fahrende Autos und noch so viel mehr
Der Einsatz von LiDAR-Sensoren erstreckt sich weit über die Automobilbranche hinaus und die Anwendungsfelder sind vielseitig. Um die Vorteile der Technologie nutzen zu können, hat Blickfeld die großen Probleme der LiDAR-Systeme aus dem Weg geräumt und sie somit für den Massenmarkt zugänglich gemacht. Die Zeit der LiDARs hat gerade erst begonnen!