MEMS-based LiDARs are a cornerstone of modern sensing technology, offering high performance and scalability. One critical component in these systems is the mirror, whose size directly impacts the functionality of the sensor. This blog post delves into the technical considerations behind the design and optimization of MEMS mirrors for LiDAR applications.
Requirements for High-Performance MEMS LiDAR Sensors
For LiDAR sensors to achieve high performance, they need to deliver long range, wide field of view, and high resolution. These requirements demand meticulous optimization of each component, including the mirrors. MEMS technology, known for its scalability and cost efficiency, provides a robust framework for designing LiDAR systems capable of meeting these demands. By leveraging silicon-based microelectromechanical systems, manufacturers can produce identical, high-quality components at scale, enabling the widespread adoption of MEMS LiDAR sensors across various industries.
Long Range Through Optimized Laser Sources
Achieving long range is a critical aspect of MEMS LiDAR sensor design. This involves optimizing the emitter and detector to ensure reliable object detection over greater distances. One starting point for optimization is the laser source. Two primary wavelengths are used in MEMS LiDAR sensors:
- 1550 nm fiber lasers, which allow for higher energy levels and longer ranges but are large, complex, and expensive.
- 905 nm laser diodes, which are compact, cost-efficient, and widely available, but are limited in beam strength due to eye safety regulations.
While the choice of emitter plays a significant role, the detector design—and specifically the aperture size—is equally crucial.
MEMS Mirrors: Finding the Optimal Size
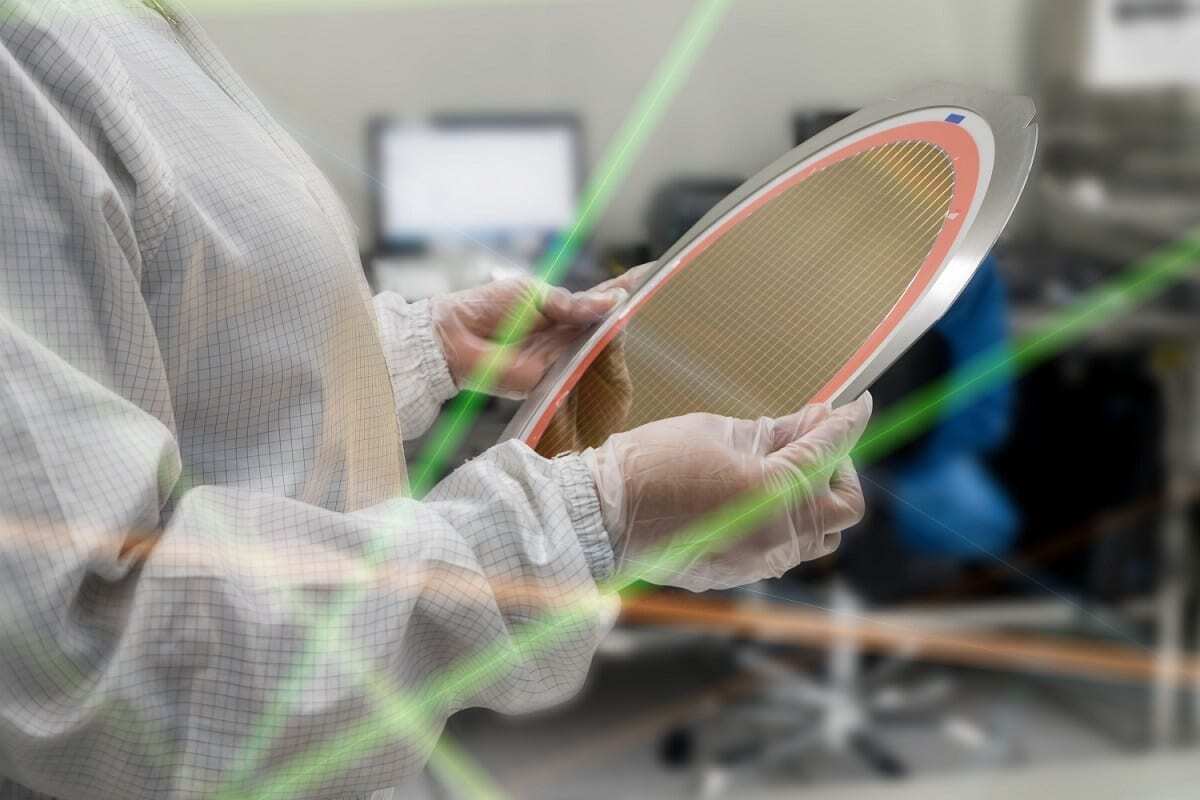
In MEMS-based LiDAR designs, the aperture size corresponds to the mirror size. Larger mirrors capture more light, enabling longer ranges and higher resolutions. However, determining the optimal mirror size requires balancing several factors:
Photon number
On the one hand, the size of the mirror depends on how many photons have to be emitted in order for a sufficient number of photons to come back to detect an object. This minimum number of photons can be calculated with good accuracy according to the link budget. This includes how many photons are lost at distance and through low reflective surfaces, homogeneous scattering of light and detector efficiency. In this way, it is possible to calculate how many photons must be emitted, i.e. how large the aperture must be so that a minimum number of photons can be detected again. In addition, Blickfeld sensors have a coaxial design, which means that only the light that comes back the same way as it was emitted is captured again. This has the advantage that no other light signals are picked up that disturb or falsify the image.
Collimation
In order to obtain high-resolution data that reliably identifies even small objects, the laser must hit an object in a collimated form. This collimation is achieved by placing a lens in front of the laser. Now the mirror size comes into play again: The mirror must be exactly large enough to deflect all the light collimated by the lens. This depends on the focal length required for optimal collimation and thus high resolution.
Resonant frequency
MEMS mirrors oscillate at a certain resonant frequency. They are triggered by integrated actuators and therefore do not require a motor or any other mechanical propulsion. This is of advantage because motors and moving parts wear out and require regular maintenance. These problems do not arise if the oscillation is triggered by integrated actuators.
The resonant frequency at which a mirror oscillates depends on the size and mounting of the mirror. For this purpose we have developed a proprietary embedding of the mirrors in order to be able to use particularly large mirrors. Due to the unusually large diameter, a large number of photons can be directed onto the scene and back onto the detector, which allows Blickfeld LiDAR sensors to achieve a long range. In addition, thanks to their size, the mirrors are more robust than conventional products, which are only a few millimeters in diameter. Yet, they have a high resonant frequency due to their lightweight construction which ensures that the photons are returned to the detector. If the mirror oscillates too quickly or too slowly, the photons are deflected past the detector due to the coaxial structure.
Tailored MEMS Technology for LiDAR
The design of MEMS mirrors for LiDAR sensors requires careful consideration of composition, size, and embedding. By focusing on these aspects, Blickfeld has developed MEMS technology specifically tailored to meet the demands of MEMS LiDAR applications, achieving long range, wide field of view, and high resolutions. This approach ensures that the sensors remain scalable, robust, and cost-effective, supporting diverse use cases.
Conclusion
MEMS technology is at the heart of modern MEMS LiDAR systems, offering the scalability and performance needed for high-precision sensing. The optimization of mirror size—considering factors like photon capture, collimation, and resonant frequency—is essential to achieving superior performance. With a focus on innovation and meticulous design, MEMS mirrors have proven to be a key enabler of advanced MEMS LiDAR technology.