More people produce more waste. The World Bank forecasts 3.4 billion tons of municipal waste per year worldwide from 2050 onwards – an increase of almost 70% on the current amount of around 2.1 billion tons. In addition to the growing population, increasing urbanization is also a driver here. These projected numbers illustrate how urgently the waste management industry needs efficient and digital waste management solutions to process these volumes of waste, as existing disposal systems are already reaching their limits.
Smart Waste Management and the Circular Economy
Effective and efficient management of waste is complex. The goal is to preserve natural resources while treating and processing waste in an environmentally sound manner, i.e., recycling as much as possible and disposing of as little waste as possible. Smart waste management thus includes not only the removal of waste but also many other steps. In addition to the collection, recording, and careful separation, it also includes reuse, recycling of reusable material, and proper disposal of non-recyclable waste. The collected waste has become an essential source of raw materials. In addition, the sale of the recovered recyclable materials is another key factor through which they return to the cycle.
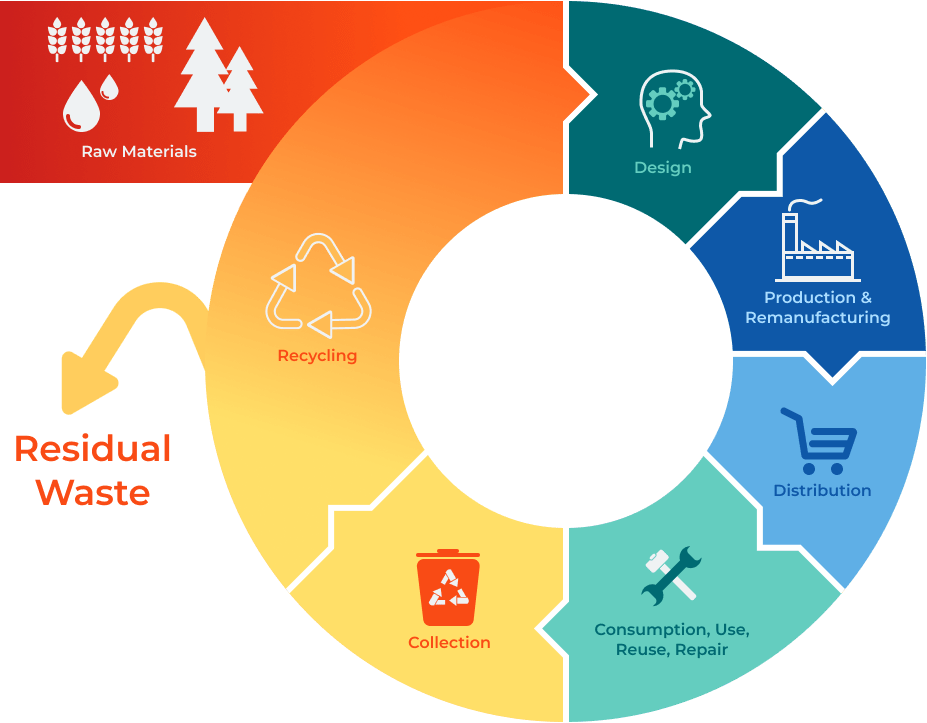
What is the Circular Economy?
The circular economy is a regenerative system that aims at extending the life cycle of products and existing materials for as long as possible through durable design, maintenance, reuse, repair, refurbishment, and recycling. Waste should thus be reduced to a minimum.
As many different parties are involved in the system, reliable data on quantities, location, or nature of the materials are indispensable in this process. Two issues, in particular, play an important role and pose challenges to intelligent waste management companies in treating and processing waste.
Safety First
Smart waste management companies must comply with a large number of regulations for the storage and recovery of waste materials. In addition, they have to implement several measures to ensure employees’ occupational safety. For instance, warehouse management has to make sure that only the approved amount of material is stored in the respective storage area or processed in the corresponding facilities. Depending on the type of material, for example, it must be stored separately according to its fire load, or safety distances between storage areas and materials need to be maintained. If companies do not comply with these requirements, this can lead to fires in the case of plastic waste due to the high fire load caused by flying sparks and thus endanger people and the environment. Furthermore, fines and penalties are expected if specifications are not complied with, which increases the financial pressure and, in extreme cases, can endanger the company’s existence.
Reducing Costs and Increasing Efficiency
Inflation combined with higher fuel and energy prices has not left the waste management industry unscathed, as companies depend on market conditions. For example, price fluctuations in the energy sector or raw materials such as plastics or paper can have a significant impact on which materials are more in demand and purchased, thus influencing the performance of companies in the market. Accordingly, the sales team for recovered materials needs to know which waste materials are in stock and in what quantities before and after processing. This enables them to react more flexibly to fluctuations in demand or market developments, e.g., by increasing the throughput of plastics. At the same time, it is essential to manage the operation of the plants in the most environmentally friendly and energy-efficient way possible to meet the increasing environmental and climate protection requirements.
For companies to master these challenges and operate efficiently, reliable data on waste flows is essential. But how is the data on waste inventory obtained?
Weighing Data and Guesstimates as Data Sources
Up to now, smart waste management companies have mainly determined the inventory of waste material flows based on the weight data of incoming and outgoing deliveries and estimates based on experience. In this context, certain deviations between the weighed incoming and outgoing material quantities are standard and are calculated from the outset. In addition, the waste piles in the storage areas are living entities as waste is regularly delivered and moved between storage areas and facilities. Process-related losses, e.g., due to inaccurate unloading, are inevitable and cause further inaccuracies. If visual estimates, in addition, come into play, there is a significant risk that the data will be distorted and not reflect an accurate image of the current warehouse situation. How data is documented also varies greatly, from an operations log within an ERP system to a mix of spreadsheets and manual notes. As a result, there is often a lack of reliable, exact data on the amount of waste in storage, making planning difficult.
Game Changer: LiDAR-based Volume Monitoring
LiDAR sensors can provide this data in combination with the corresponding perception software. The laser-based technology continuously generates data and summarizes it in high-resolution 3D point clouds as an exact image of the environment.
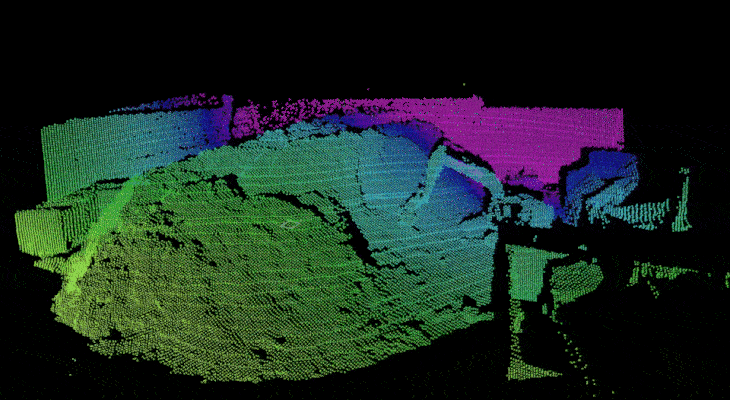
The LiDAR sensors thus create a detailed image of the waste pile surface, which serves as the basis for the volume calculation. The measurement can be performed with stationary devices thanks to the wide field of view and long range. This is a significant advantage over other technologies, such as radar or single-point laser sensors, which, for example, have to be set up at different measurement points to cover the entire pile. Combining data from multiple measurements is time-consuming and significantly delays data provision. With LiDAR solutions, point clouds from multiple sensors can be easily merged in the software, and thus even large stockpiles can be monitored reliably and continuously.
Implementation in Smart Waste Management
For example, the sensors can be easily integrated into the existing infrastructure of a storage area of a material recovery facility. They are mounted to overlook the storage boxes of the waste piles. To ensure that the walls of the boxes are not detected, zones are set up in the point clouds in the corresponding perception software, within which the volume is detected. As soon as, e.g., a wheel loader unloads or removes waste in a zone, the software immediately calculates the new volume.

The zones can be configured as needed for an entire pile or only for a specific area. This can also trigger a notification if, for example, the maximum allowed storage volume per box or even the total waste is reached, or the inventory is too low to keep the system running efficiently.
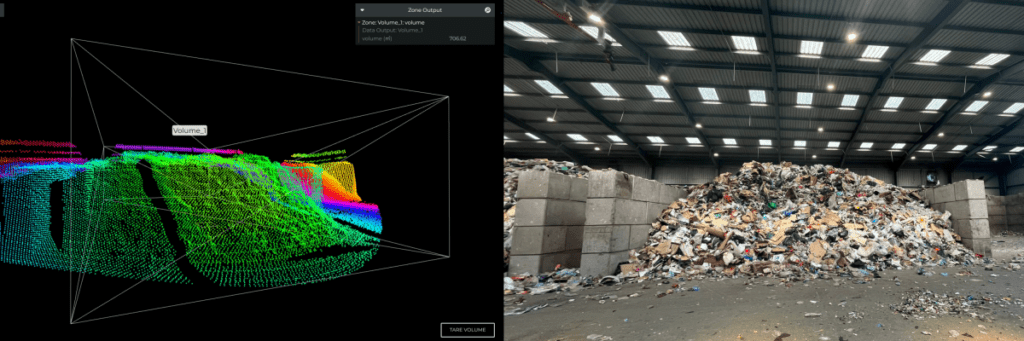
Efficient Waste Storage Management
Smart waste management companies can access the real-time data on-demand via a dashboard and, if required, also integrate it directly into an ERP system. In so doing, they can keep an eye on their inventories across the site, from the storage areas to the sorting or for sale area, and adjust their inventory levels more flexibly to market conditions. As a result, the sales department benefits from a better planning basis and can dispatch logistics according to demand.
At the same time, the digital monitoring of stock levels in various plant areas enables smart waste management companies to see where losses are occurring in the treatment chain and optimize processes accordingly. Moreover, this saves time and effort, as manual inventory estimates and calculations with post-correction become obsolete – a glance at the dashboard is all that is needed. Above all, the data obtained by LiDAR enables companies to meet their compliance obligations more easily, act more sustainably, and optimize accounting accuracy.
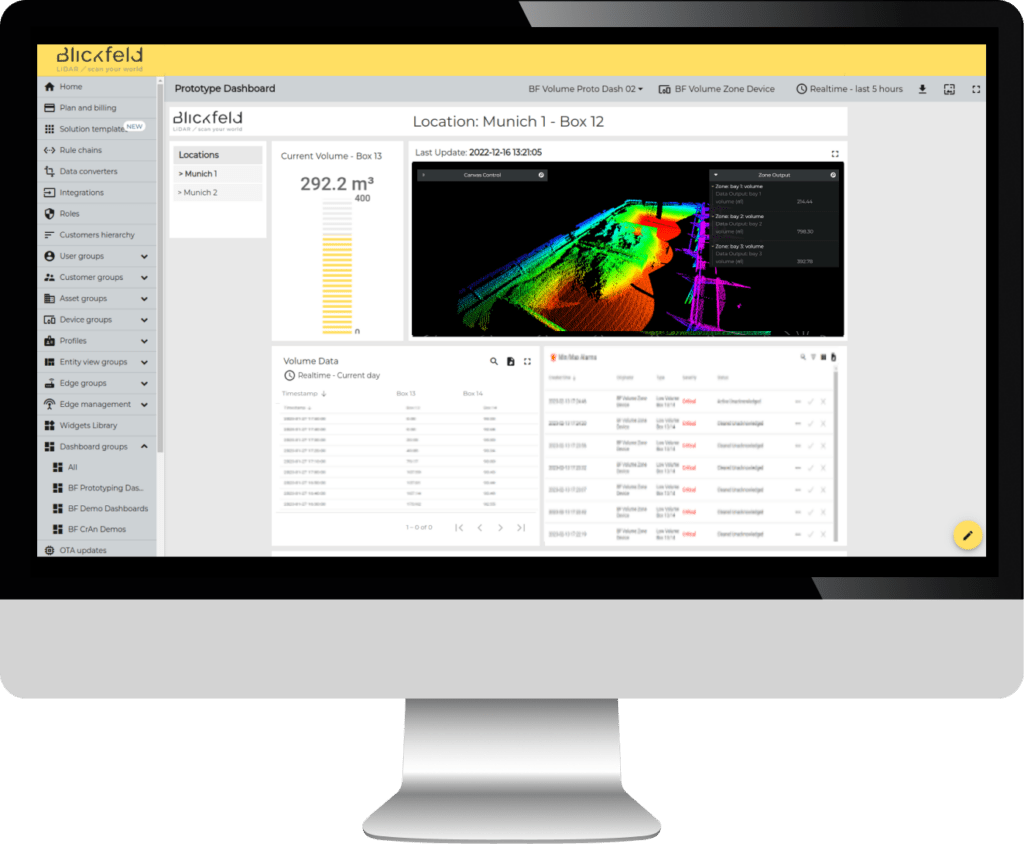
Smart Waste Management 4.0 Thanks to LiDAR
The implementation of LiDAR-based volume monitoring can significantly support companies in the smart waste management sector in making their processes more efficient and sustainable. Digital real-time data on waste inventories create transparency and enable more flexible and demand-oriented operations for all parties involved in the circular economy. Therefore, LiDAR technology in warehouse management makes an essential contribution to digitization and process optimization in Digital Waste Management and Intelligent Waste Management.
Success Story
Cireco (Scotland) LLP, a leading company for complete resource management, works with volumetric measuring specialist Quvo Limited in deploying Blickfeld LiDAR sensors for stockpile monitoring. The automated volume monitoring solution provides the company with accurate data on the amount of waste stored in bunkers before sorting. The real-time data not only improves the utilization of the materials recovery facility but also provides the accounting and logistics departments with a reliable source of data to more easily comply with material storage regulations for safety and risk reasons.
Read more about Cireco