The vulnerability of global supply chains has been demonstrated several times in recent years. Whether it is a tanker getting stuck in the Suez Canal, blocking traffic through the strait for several days and significantly disrupting international materials trade, or a lack of raw materials as a pandemic brings factories to a standstill for months. There are always events that disrupt the global exchange of goods.
These examples are serious events constituting significant incidents for many companies around the world, but the fundamental issues can be applied to every single supply chain, including those within companies: Stakeholders and processes interlock in a supply chain like a cogwheel, meaning that inaccuracies and deviations quickly affect the entire supply chain. A small error can easily multiply and cause financial damage – the same applies to both global supply chains and internal supply chains of medium-sized companies.
To avoid this issue, efficient stockpile inventory management plays a key role for many companies. The focus of such management systems is placed on ordering, storing, and using materials with the aim of keeping inventories as low as possible and delivery capability as high as possible. Inventories are bound costs while simultaneously being the most important capital for companies. Efficient and effective stockpile inventory management is therefore critical to success, representing a core task in supply chain management.
Stockpile Inventory control and monitoring is an important aspect here: In order to manage inventory successfully, it is necessary to record exactly where and how much material is available. Especially companies working with bulk materials, such as gravel or sand, often do not have this data at hand because they lack a precise monitoring system.
How much material is currently in stock?
The answers to this question are often inaccurate despite recording methods such as truck scales. But why? This can be well illustrated by an example.
A building materials company specializes in both the sale of gravel and sand and the production of concrete. In preparation for production planning, the company discovers that there is a shortage of gravel in the warehouses. However, according to the inventory documentation and accounting, there should be enough material for processing. The company has to buy gravel at short notice at a high price and reschedule so that the production of concrete can be kept running and customers can be supplied with gravel. So how did the material shortage come about? A look at the supply chain can provide insight.
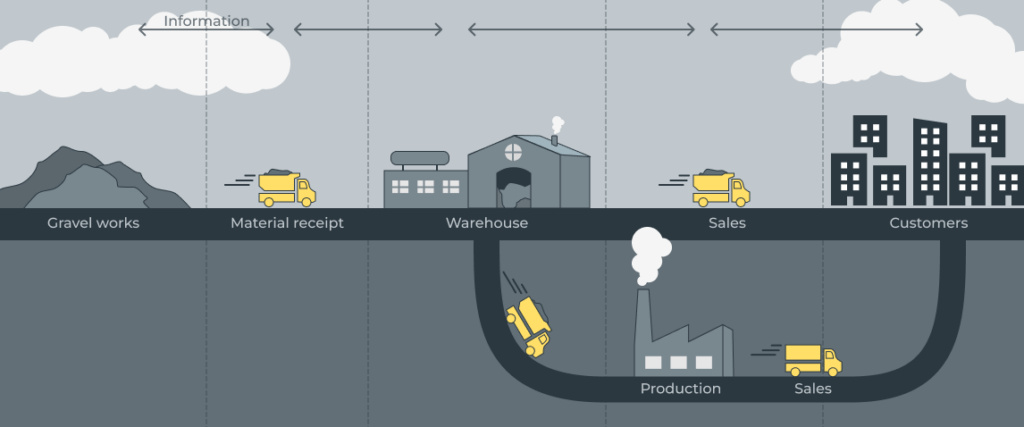
The company procures gravel from its own gravel works, which transport the bulk material by trucks to a large warehouse every day after processing. There the gravel is stored for further processing, as well as for direct sale. Upon arrival, the cargo is weighed using truck scales in the delivery zone. Errors or slight inaccuracies are normal with weighing systems and are taken into account, but the truck scales of the building materials company were calibrated some time ago, and therefore the weighing data is no longer particularly accurate. In addition, external factors can influence the data, such as rain, which causes the gravel to be delivered wet and distorts the weight accordingly. This is where decisive inaccuracies creep in as early as the delivery stage.
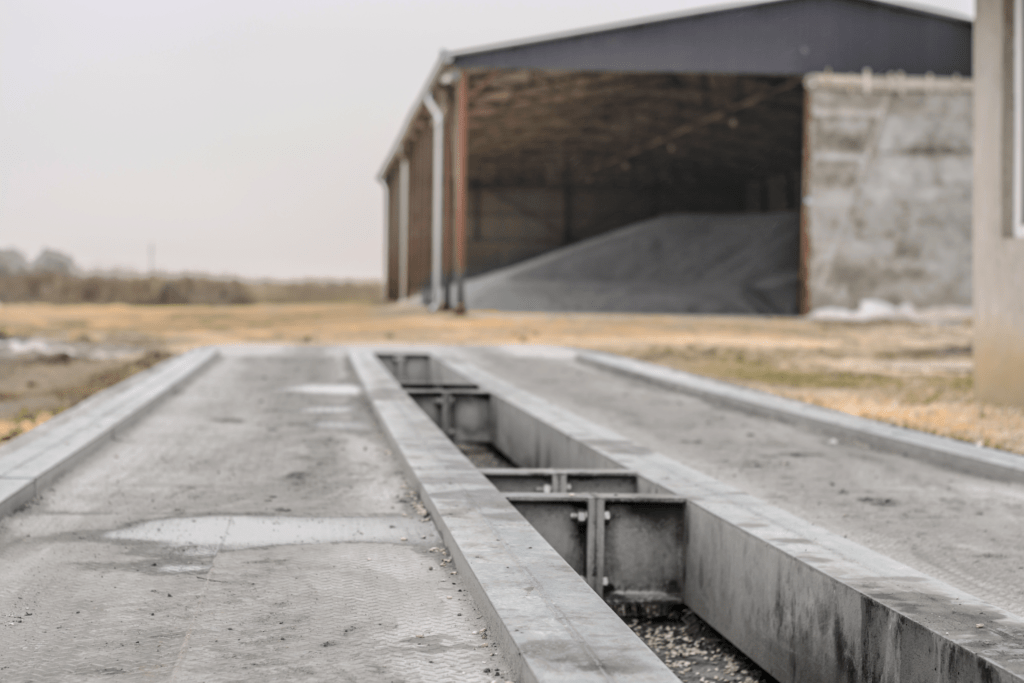
Eyeballing stock allocation
After weighing the trucks, the data is recorded in the inventory documentation and the gravel is placed in large storage boxes for processing or direct distribution. A warehouse employee visually estimates the current stock to distribute the material to the boxes. Based on this estimate, the gravel is unloaded into the respective boxes. There is often a residual amount left in the loading area when unloading the material, especially if the gravel is wet. So the truck takes some of the material back with it, and further discrepancies arise between the recorded and the actual quantities in storage.
In addition to measurement errors caused by scales, bulk material is often estimated visually or calculated on a truck-by-truck basis, which can be rather inaccurate. As a result, deviations of up to 10-15 percent can already occur during delivery and even 20-30 percent when estimating by eye.
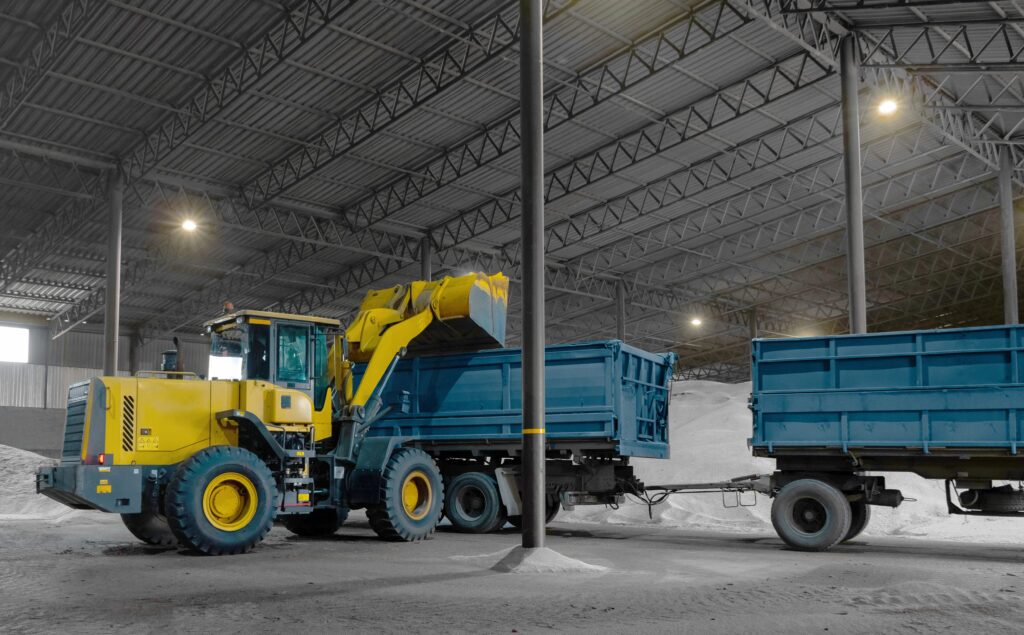
Storage is not the last potential source of error: In the case of outgoing material, either for further processing or for direct sale, the quantity of product in the building materials company is also documented with a lack of precision. For transportation, the company loads the gravel onto trucks with an excavator. The weight of the material is recorded and documented by the scales in the buckets. As with delivery, material losses occur during loading because e.g. the buckets are not completely emptied, resulting in discrepancies in the inventory documentation.
Inaccurate data collection distorts stockpile inventory documentation
Since inaccuracies have crept into the inventory recording during material receipt and distribution, as well as during goods issue, the accounting data deviates greatly from the actual quantity stored in the boxes. This ultimately leads to the fact that according to the system, there is still material available for production, but the boxes are as good as empty. To fulfill customer orders, the company thus has to buy gravel at short notice, which entails increased costs, a higher workload, and delivery delays. The shortage of materials affects not only the internal processes of the building materials company. There is a lack of accurate, reliable (real-time) data on material receipt and inventory in the warehouse. If this information is already inaccurate from the beginning or even missing completely, it impacts the entire supply chain of companies, as seen in our example.
Volume monitoring based on LiDAR technology can be a solution to this widespread challenge.
Volume monitoring with LiDAR
3D LiDAR sensors are based on the time-of-flight principle. They emit light pulses into the environment, detect the light reflected from the objects, and calculate the exact distance based on the time of flight. This process is repeated hundreds of thousands of times per second and the results are combined into a 3D point cloud.
In the warehouse, the sensor system scans the entire surface of the material piles in this way and generates a detailed image consisting of thousands of data points that map every variation in the surface. Based on this data, the volume of material piles is calculated. LiDAR thus has a significant advantage over other common sensor technologies used for volume monitoring, such as single-point lasers or radar sensors. These solutions do not allow complete 3D imaging of the surface or can only capture the entire material in a very complex and costly manner using multiple devices or measurements.
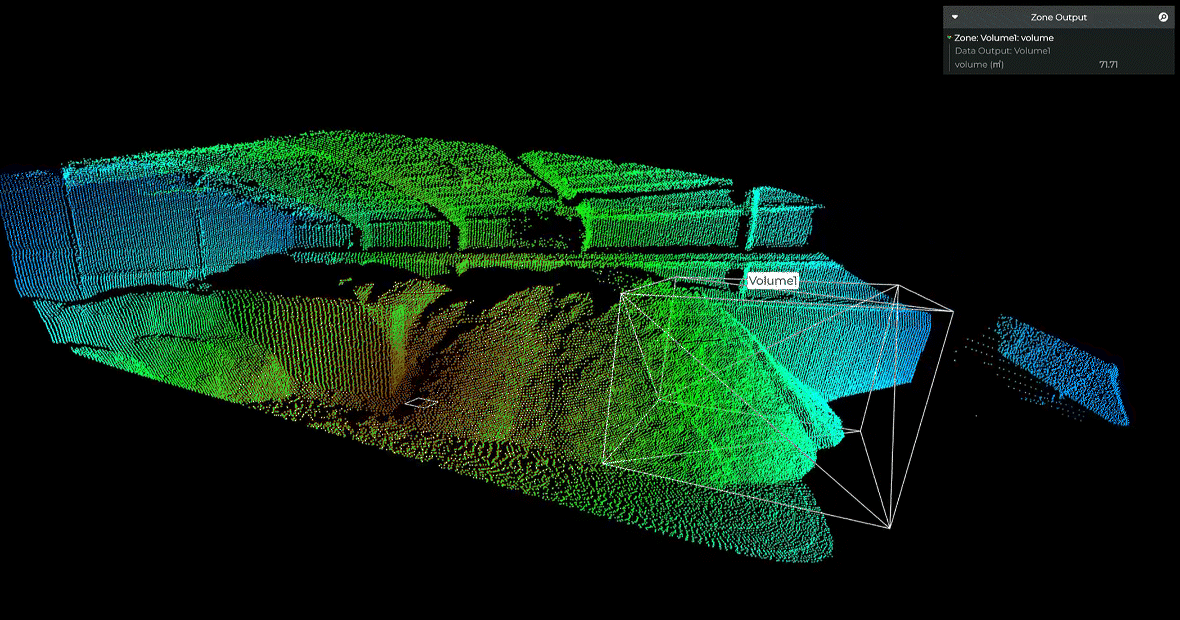
In our example, the laser-based LiDAR sensors for detecting the material in the facility are mounted on the ceiling to overlook both the unloading zone and the gravel storage boxes. In the associated perception software, zones are set up in the point cloud within which the volume is detected. This ensures that only the volume of the actual material is calculated and not additional volumes, for example, that of the walls that border the boxes.
As in many warehouses where bulk materials are stored, the building materials company’s hall is sometimes very dusty due to the movement of the gravel, and some areas are poorly lit. This is a challenge for volume monitoring technologies such as photometry, as they depend highly on lighting conditions. LiDAR sensors, on the other hand, do not require ambient light, which means that the technology is fully functional even in unlit areas of warehouses or outdoors at early dusk.
Efficient stockpile inventory management through accurate, reliable real-time data
The sensors continuously collect data. As soon as a truck or excavator unloads or removes gravel in a zone, the change in volume is calculated by the software. A dashboard displays the volume of bulk material in real-time or provides the data on demand. Either the total volume of the pile can be recorded or the zone is tared before delivery so that only the newly delivered material is recorded, allowing the system to be adapted to individual needs.
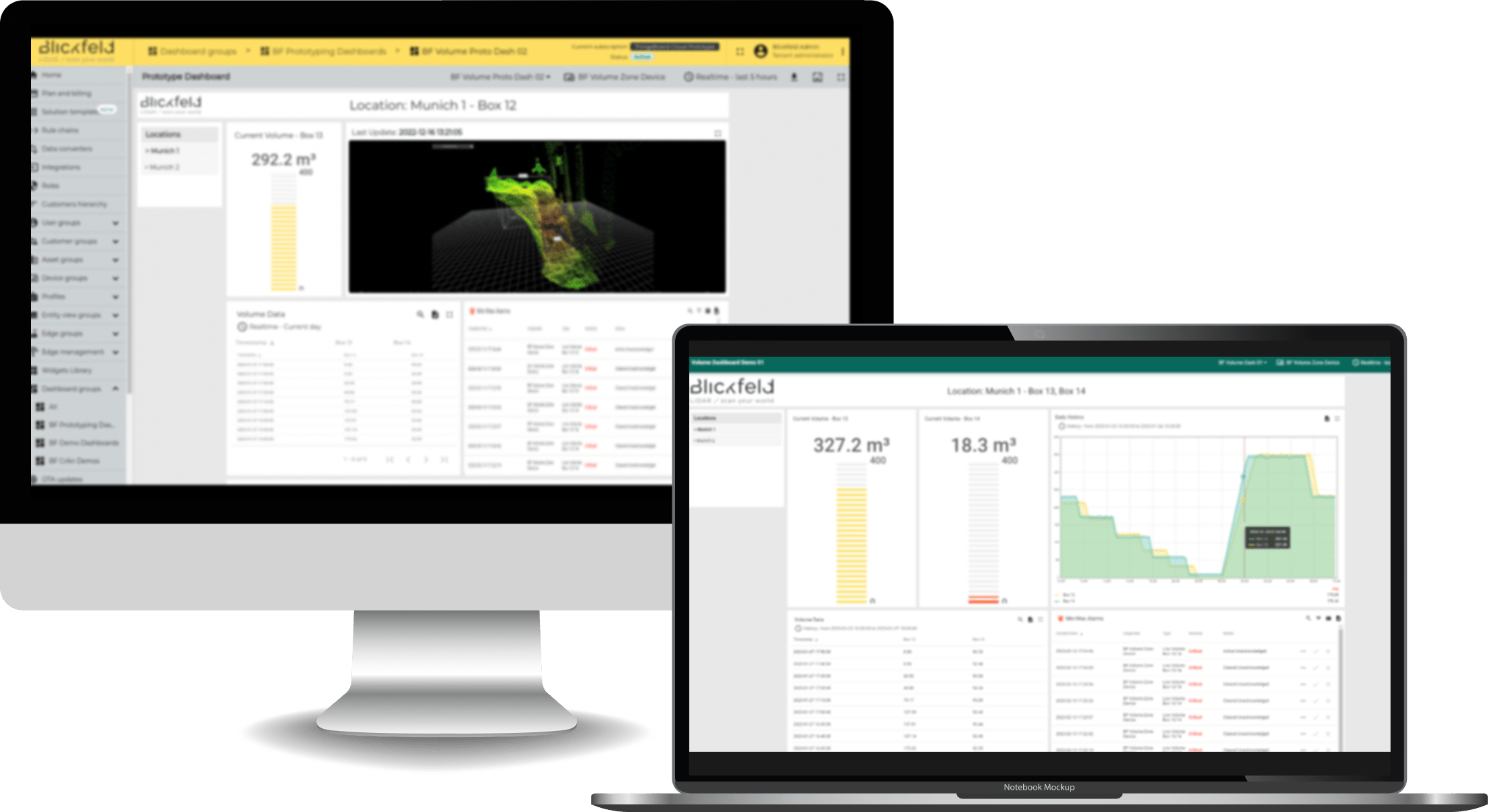
The company in our example can accurately track inventory at any time via the dashboard using the zones in the delivery area, as well as in the storage boxes. This not only saves time and effort, as previous, time-consuming documentation and estimates become obsolete but also enables better control of the inventory. Gravel shortages and surpluses can be anticipated by the company in a timely manner by ordering more gravel or reallocating material as needed.
Real-time data creates transparency for all parties involved, from purchasing and production to accounting and sales, keeping the company’s supply chain in flux, which has a positive impact on efficiency and ultimately customer satisfaction
On the way to Supply Chain 4.0 thanks to LiDAR
Reliable, digital stockpile inventory data is a basic requirement for efficient stockpile inventory management, which is precisely what smart LiDAR sensors provide in real-time. They enable improved and targeted demand, production and distribution planning as companies know exactly how much material is available in the warehouse and when, allowing them to respond more flexibly to fluctuations. At the same time, they can position themselves more efficiently in both warehouse management and the sale of bulk materials. The data obtained through LiDAR creates transparency that is often missing at the very beginning of the supply chain. Accordingly, the use of LiDAR technology for inventory recording makes an important contribution to the digitalization and optimization of the supply chain.