Accurate, real-time data on raw material stockpiles is pivotal in optimizing the entire cement production supply chain. Precise stockpile information enables better forecasting, inventory management, and resource allocation. This capability helps cement plants reduce material waste, minimize downtime, and improve production scheduling. When integrated with other digital strategies, real-time stockpile insights contribute to a more agile and responsive supply chain, better equipped to meet market demands and enhance overall operational efficiency.
The Qb2 LiDAR Sensor captures high-resolution 3D data. The on-device software analyzes this data directly on the device and outputs precise volume information on request.
Overcoming Industry Challenges
Raw Material Availability and Supply Chain Disruptions
A significant challenge in the cement industry is managing the availability of raw materials and addressing supply chain disruptions. Cement production relies on a variety of raw materials, including limestone, clay, and gypsum. Factors such as geopolitical issues, natural disasters, and logistical inefficiencies can lead to material shortages and production downtimes or overstocking. Effective inventory management is essential for identifying potential issues early, enabling proactive measures to mitigate their impact.
Traditionally, stockpile management has relied on manual estimates and periodic checks, such as visual assessments or counting deliveries. However, even experienced personnel can make inaccurate estimations. While periodic checks provide a snapshot of inventory levels at specific moments, they fail to offer real-time, accurate data. This gap means that cement companies often lack a precise understanding of their actual stock levels between measurements, contributing to several pain points:
- Ordering Errors: Incorrect quantities of raw materials or transportation can lead to unnecessary costs and delays.
- Material Shortages: Running out of essential materials, like clinker or additives, can halt production and disrupt operations. This is particularly critical since the production of clinker is energy-intensive and requires consistent material input.
- Environmental Impact: Poor planning can lead to excessive CO2 emissions from additional transport runs and inefficient resource use.
Embracing Cement Plant Digitalization
To improve inventory management in cement production, Blickfeld’s LiDAR sensors offer a precise method for measuring raw material stockpiles. These sensors use laser pulses to scan material piles with centimeter-level accuracy, creating detailed 3D models composed of millions of data points. The integrated software then calculates the volumes of these stockpiles, and by incorporating material density information, it determines the exact tonnage of the stored materials.
This data is automatically fed into inventory management systems or made accessible through a dashboard, providing up-to-date information across various sites and materials. The system supports both real-time and on-demand monitoring, allowing for continuous measurement or specific intervals, such as daily checks, depending on operational needs.
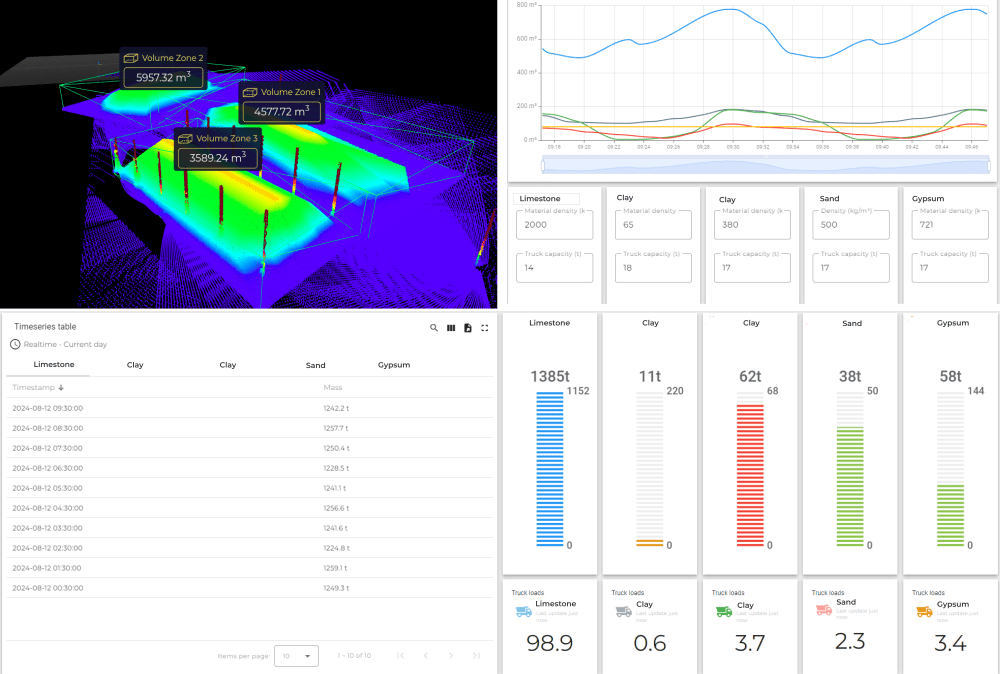
In terms of infrastructure, Blickfeld’s sensors utilize a single cable for both power and data, which reduces setup complexity and installation effort, and improves reliability. Standard data interfaces facilitate integration with existing digital platforms, addressing the operational requirements of cement production effectively.
Benefits of Digital Stockpile Management for Cement Producers
Introducing real-time stockpile data brings several significant advantages to cement factories, enhancing operational efficiency and decision-making across various aspects of production and logistics:
- Preventing Material Shortages: Real-time stockpile data ensures that raw materials are always available in the required quantities. By continuously monitoring stockpile levels, cement factories can avoid unexpected shortages that could halt production. With accurate data, factories can automate the ordering process, triggering replenishments as soon as stock levels reach a predetermined threshold. This automation aligns material availability seamlessly with production schedules, reducing the risk of delays and keeping operations running smoothly.
- Optimized Truck Fleet Management: With precise stockpile data, factories can determine the exact number of truckloads needed for material transportation. This reduces the risk of over- or under-ordering transport vehicles, leading to more efficient logistics operations. By aligning truck deliveries with actual inventory needs, factories not only minimize transportation costs and improve delivery schedules but also reduce unnecessary fuel consumption and emissions.
- Effective Storage Space Management: Real-time data helps in assessing whether existing storage space is sufficient for the cement being produced. Accurate inventory information allows plant managers to plan for adequate storage capacity, avoiding congestion and ensuring that space is efficiently used for both raw materials and finished products.
- Automated Stock Distribution: Advanced stockpile management systems can automate the distribution of raw materials to various storage locations based on real-time data. This dynamic allocation optimizes storage space and ensures that materials are placed in the most suitable locations, improving overall operational efficiency and reducing handling time.
- Enhanced KPI Reporting: Real-time stockpile data enables more accurate and timely reporting of key performance indicators (KPIs). Cement factories can track metrics such as inventory turnover, material usage rates, and production efficiency. This data-driven approach supports better strategic planning and operational adjustments, leading to improved performance and profitability.
Dust and Particulate Matter: A Unique Challenge in Cement Plants
Dusty environments are a common challenge in cement plants, where airborne particulate matter can interfere with equipment performance. Blickfeld’s LiDAR technology is specifically designed to operate effectively in these harsh conditions. It features dust-resistant enclosures and self-cleaning mechanisms that help maintain consistent and reliable operation, even in the presence of heavy dust.
Sustainability in Cement Production
Sustainability is a critical focus for the cement industry. Digital tools that provide precise stockpile data play a significant role in advancing sustainability efforts:
- Reduced CO2 Emissions: Accurate stockpile management allows companies to precisely determine the number of truckloads needed, reducing excessive transportation, fuel consumption, and emissions. Since cement production is a major source of CO2, optimizing transportation and material handling can significantly contribute to lowering the carbon footprint.
- Efficient Resource Use: Better management of storage space and balanced production schedules conserve raw materials and energy, which is critical given the energy-intensive nature of cement production.
Future-Proofing Cement Operations
As digitalization continues to advance, cement producers must prepare for future industry trends and regulations. The integration of digital solutions is not just about addressing current challenges but also about positioning companies for long-term success.
- Upcoming Regulations: Future regulations may impose stricter standards on emissions and resource usage. Adopting digital tools now will help companies stay ahead of these regulations and maintain compliance.
- Technological Advancements: The pace of technological innovation is accelerating. Embracing digitalization today will ensure that cement producers are well-positioned to leverage future advancements and maintain a competitive edge.
Conclusion
Cement plant digitalization, particularly through precise stockpile volume monitoring, addresses some of the most pressing challenges facing the cement industry today. By adopting advanced technologies like Blickfeld’s LiDAR sensors, cement producers can enhance efficiency, reduce environmental impact, and achieve significant cost savings. Furthermore, integrating digital solutions can improve material quality and production consistency, which are essential for maintaining competitiveness in a rapidly evolving market.