LiDAR Solutions for a safe and efficient digital world
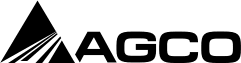

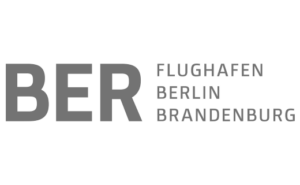


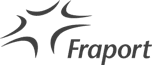

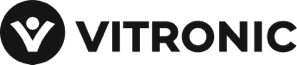
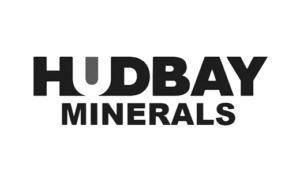
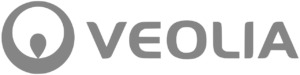
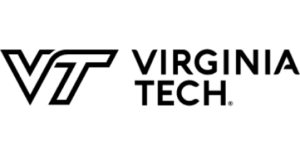

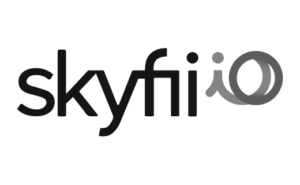
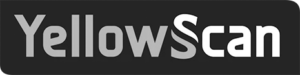
Blickfeld LiDAR
Discover Blickfeld’s latest sensor generation: High-precision 3D LiDAR technology combined with intelligent perception software – for reliable object detection and real-time analysis.
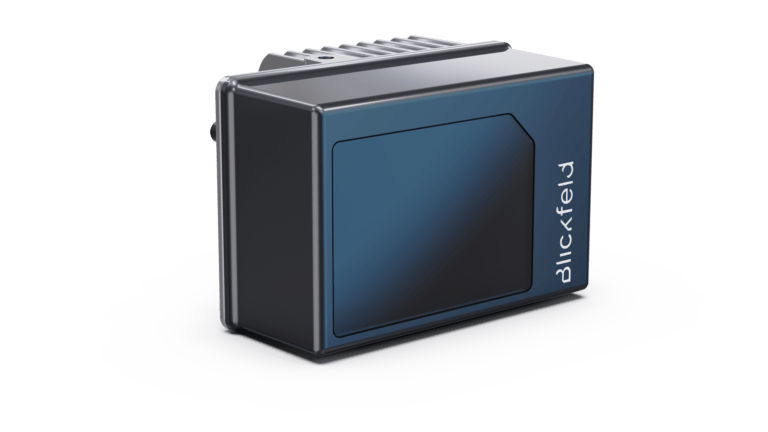
Qb2
3D LiDAR with on-device data processing – suitable for intelligent applications such as people flow analysis, traffic monitoring, and industrial automation.

QbBasic
3D LiDAR sensor for reliable point cloud acquisition – designed for OEMs and system integrators implementing their own data evaluation.
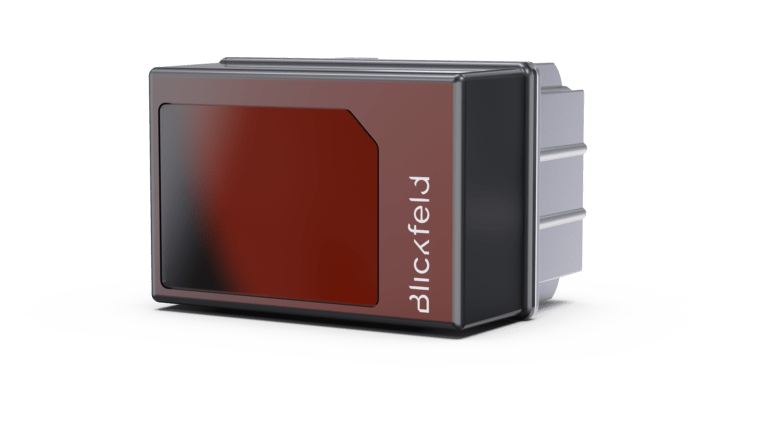
QbProtect
3D LiDAR for security applications – reliably detects intrusions using on-device processing and precise outdoor detection.

QbVolume
3D LiDAR for volume measurement – delivers precise, needs-based data for efficient inventory and logistics management.
Case Studies
Blickfeld LiDAR solutions enable a host of applications in various different industries.
Application Areas
Company news
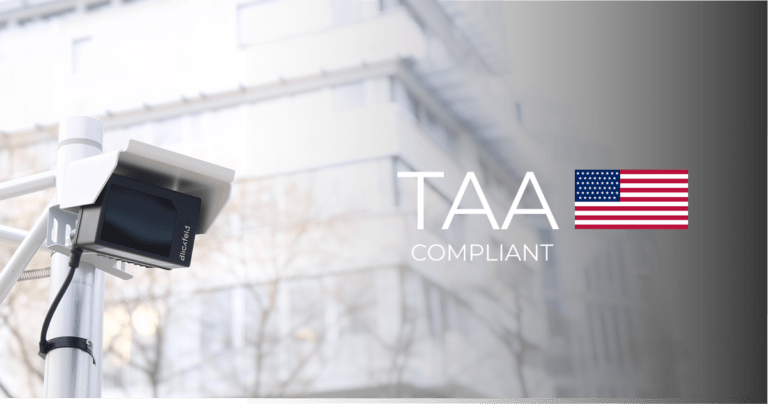
Blickfeld strengthens international competitiveness with TAA-compliant Qb product portfolio
Blickfeld continues to strengthen its international presence: The entire Qb product portfolio — including Qb2, QbProtect, QbVolume, and QbBasic — is now available in compliance
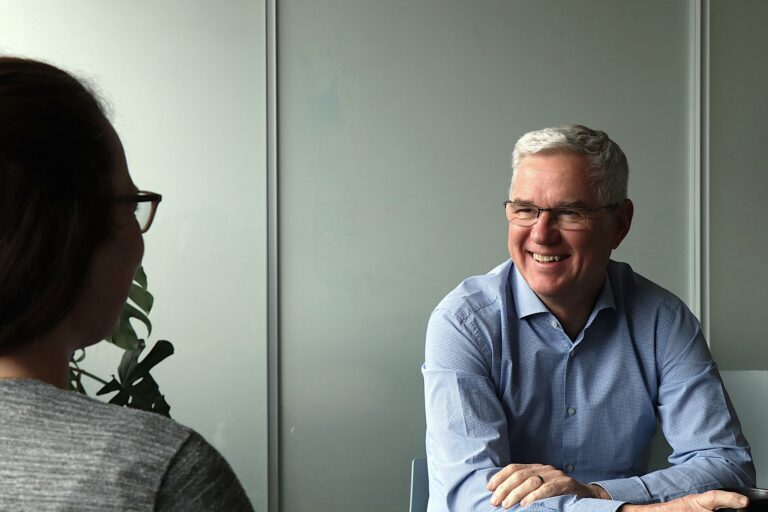
“Even the best product doesn’t sell itself.”
Interview with Dirk Rathsack – VP of Business Development & Sales at Blickfeld Dirk Rathsack joined Blickfeld nearly a year ago as Vice President of
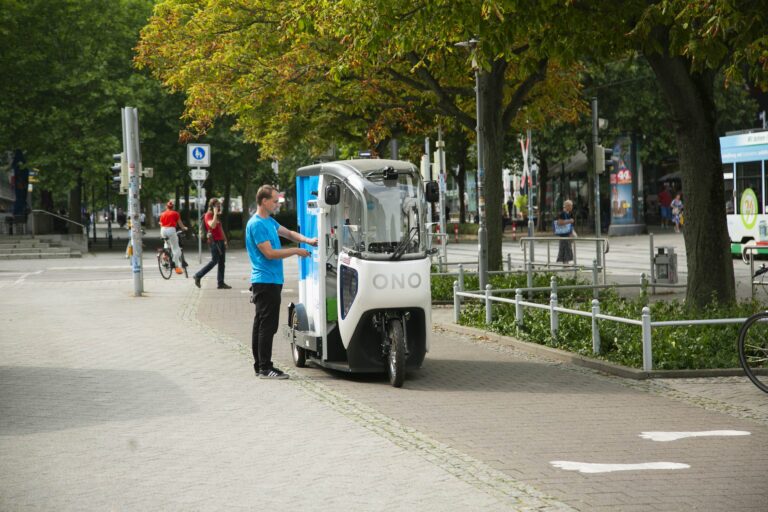
How can parcel and mail deliveries in urban areas become more efficient, flexible, and sustainable? That’s the driving question behind a visionary project exploring the
Newsletter
Be the first to receive:
- Updates on the latest developments at Blickfeld
- Exciting blog posts and interviews
- Direct access to data sheets, whitepapers and more
By subscribing to the newsletter of the Blickfeld GmbH you agree to our Privacy Policy and to the tracking of your opening rates.