LiDAR Solutions for a safe and efficient digital world
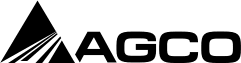

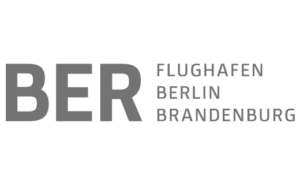
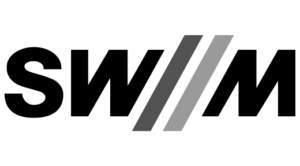
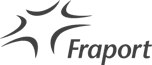
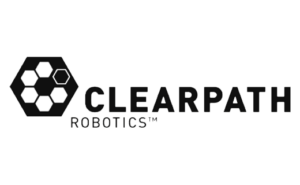
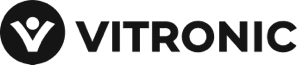
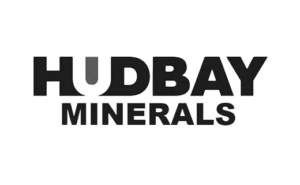
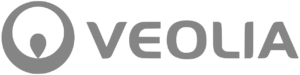
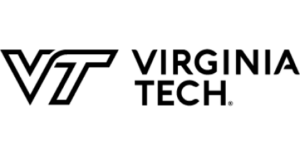

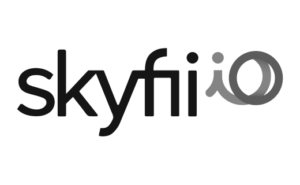
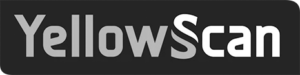
Blickfeld LiDAR
Meet Blickfeld's latest sensor generation: Cutting-edge LiDAR technology combined with powerful perception software.
Qb2
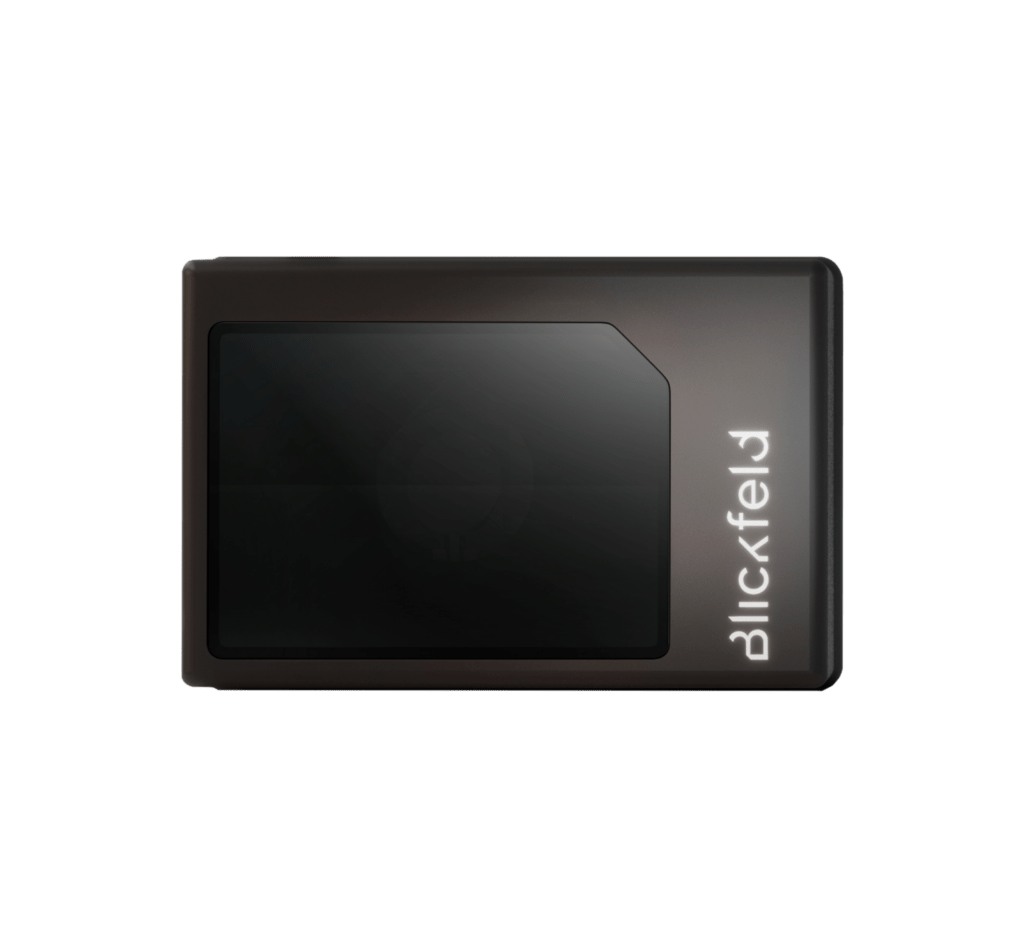
Industry-first smart 3D LiDAR combines high-performance sensing with advanced on-device processing
QbProtect
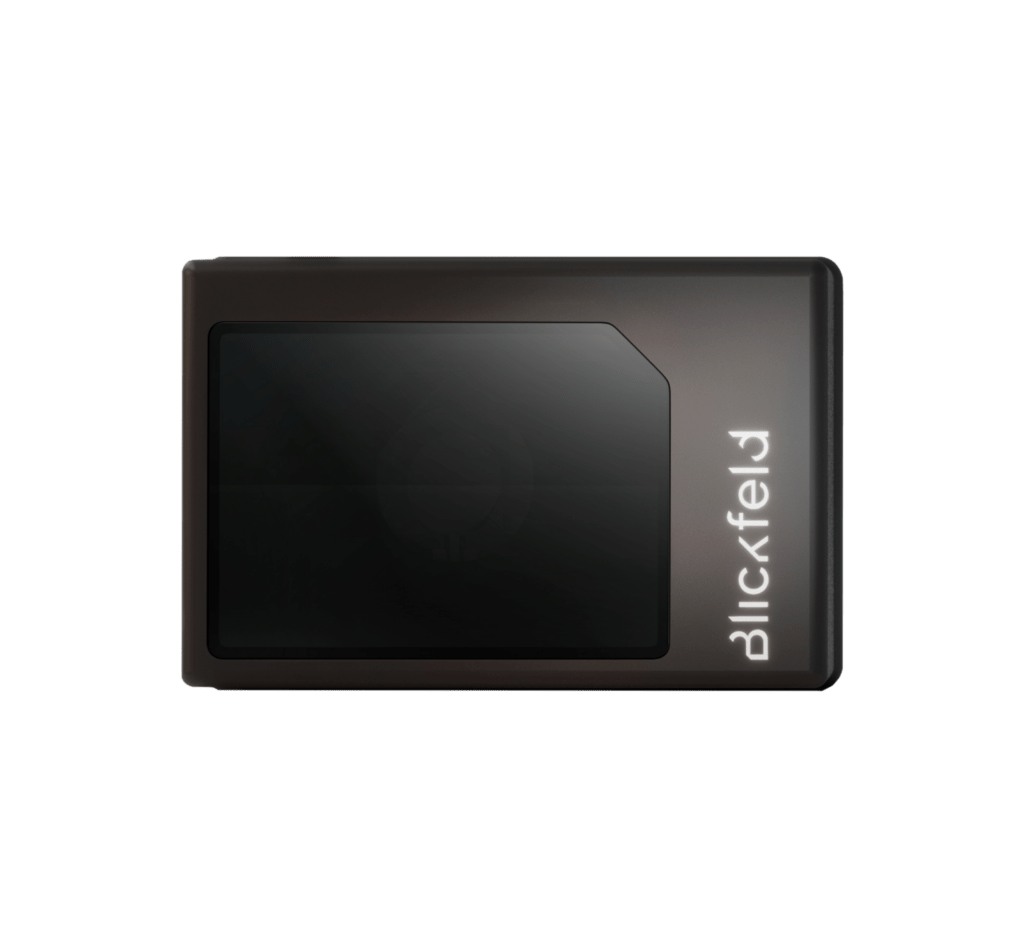
Smart 3D Security LiDAR with on-device data processing for advanced physical security applications
Case Studies
Blickfeld LiDAR solutions enable a host of applications in various different industries.
Application Areas
Company news
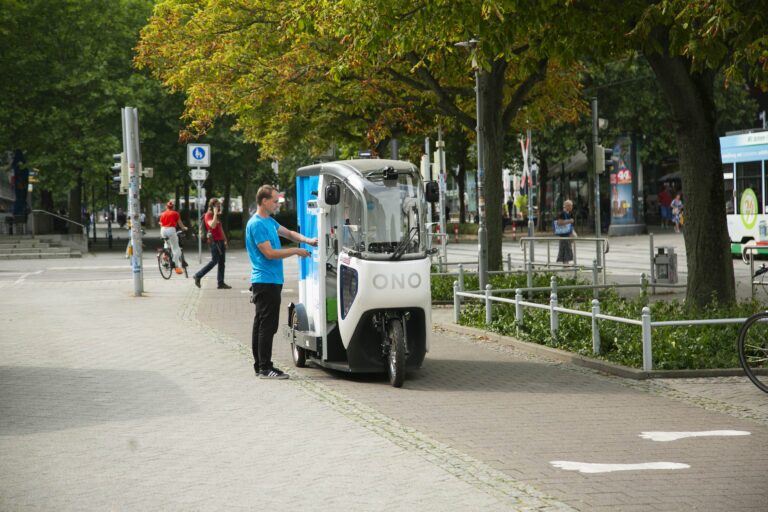
How can parcel and mail deliveries in urban areas become more efficient, flexible, and sustainable? That’s the driving question behind a visionary project exploring the
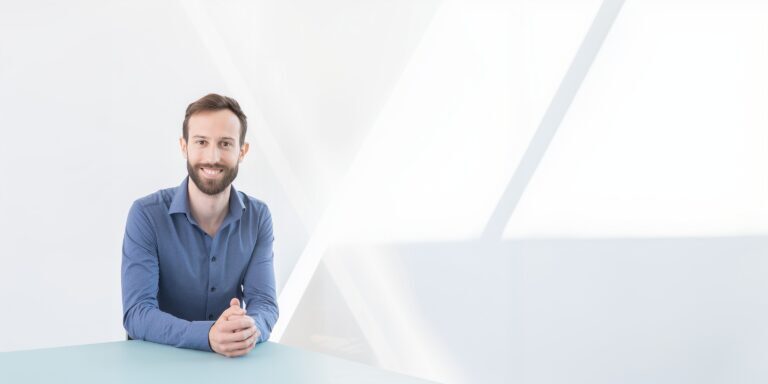
Blickfeld Strengthens Market Position with New Security Business Unit
With the establishment of its Security Business Unit, Blickfeld is responding to the growing demand for innovative security solutions. This strategic move focuses on the
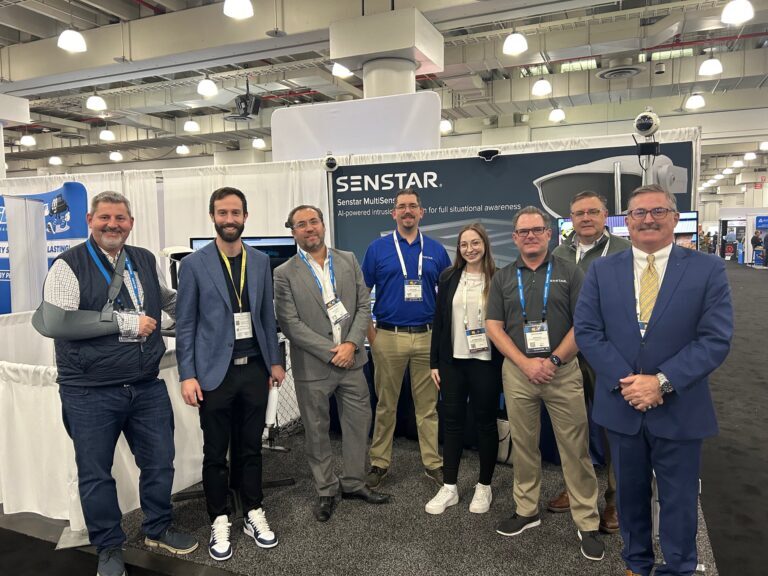
Senstar and Blickfeld Announce Global Expansion of Partnership
Senstar and Blickfeld expand their partnership from Europe to a global scale, enhancing their ability to deliver advanced 3D LiDAR security solutions for intrusion detection
Newsletter
Be the first to receive:
- Updates on the latest developments at Blickfeld
- Exciting blog posts and interviews
- Direct access to data sheets, whitepapers and more
By subscribing to the newsletter of the Blickfeld GmbH you agree to our Privacy Policy and to the tracking of your opening rates.